PVC sheets are essential materials across various industries due to their versatility, durability, and cost-effectiveness. From construction projects to DIY crafts,
needing PVC sheets cut to specific sizes is common. Whether it's for commercial use or personal projects, precision in cutting ensures the optimal utility of these sheets and contributes to the overall quality of the project.
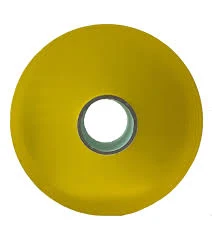
Having spent years working with and sourcing PVC sheets for various applications—from intricate craft projects to large-scale industrial installations—my experience has endowed me with insights into the critical aspects of obtaining the best precision cuts. Proper selection and understanding of these sheets are vital for anyone looking to maximize their benefits.
Experience with PVC Sheets
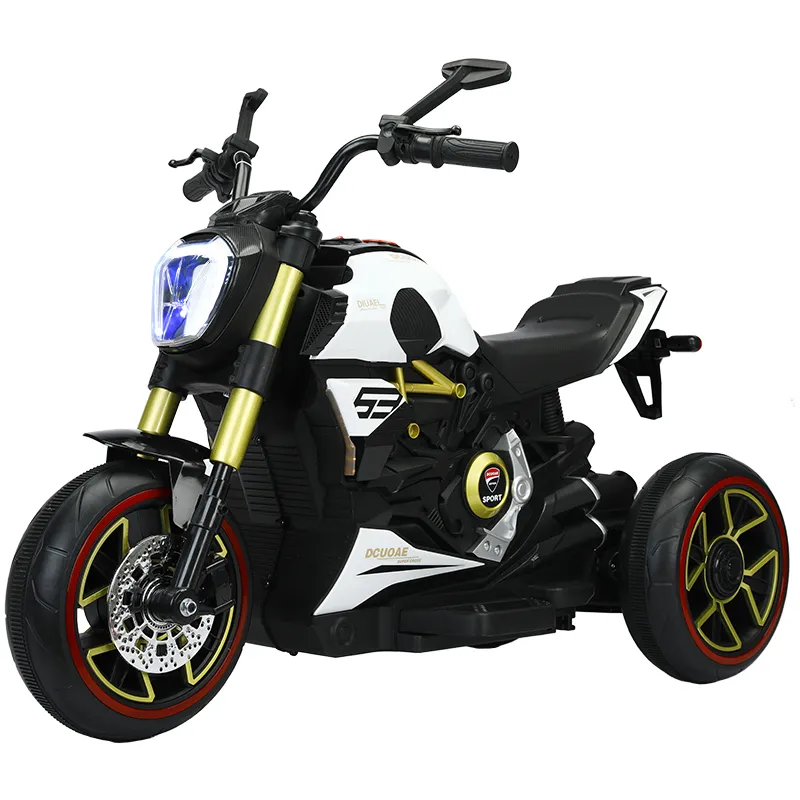
In my hands-on experience, proper planning before cutting is crucial. PVC, being both flexible and sturdy, requires careful handling. An understanding of the material's thickness and intended use guides the decision on cutting tools and techniques. For example, thinner sheets are perfectly sliced using a sharp utility knife, while thicker and more robust sheets demand tools like table saws equipped with fine-toothed blades for smooth and accurate cuts.
A common mistake I have observed is underestimating how PVC sheets react to temperature changes. When cutting, friction can generate heat, potentially causing the material to warp. To mitigate this, I recommend frequent breaks during extended cutting sessions and regular calibration of tools to handle the thermal expansion efficiently.
Expertise in Precision Cutting
Precision is key in ensuring parts fit together seamlessly in your project. Having previously overseen a variety of projects where accuracy was non-negotiable, my expertise underscores the importance of measurement and marking accuracy. Using high-quality measuring tools like T-squares or laser measures can drastically improve cut precision. Moreover, marking should be done using non-permanent methods such as a pencil or masking tape to avoid permanent marks on the PVC surface.
Investing in quality tools cannot be overstated. A clean, square edge is often the hallmark of professional work and is achieved only through well-maintained and appropriate equipment. Whether using a hand saw or a high-end laser cutter, regularly checking the calibration and blade condition ensures each cut's precision and reduces material wastage, leading to cost-effective project management.
pvc sheet cut to size
Authoritativeness on PVC Handling
Having worked with numerous clients in industries like aerospace, construction, and retail, my recommendations often reflect a collective knowledge and adherence to industry best practices. PVC’s adaptability extends from being used in signage to its application in airfreight logistic trays. Regardless of the usage scenario, one authoritative tip is to always align the cutting process with the final application—considering factors like environmental exposure and load-bearing requirements.
Developing authoritative content or instructional guides on PVC sheet handling and customization can significantly aid hobbyists and small business owners. Such resources often emerge from pooling industry insights and proven methodologies that streamline and optimize the end-user experience.
Trustworthiness in PVC cut-to-size service
Trust comes from consistent results and reliability in your service or ability to DIY. It's essential to work with vendors or service providers with a proven track record of delivering precisely cut PVC sheets. Certifications, client testimonials, and a robust portfolio serve as indicators. Where available, opting for suppliers who provide on-site visits or consultations can significantly enhance trust, as firsthand inspections are invaluable in ensuring material quality.
For those undertaking personal projects, taking the time to perfect your cutting technique builds trust in your skillset. By practicing on scrap pieces before committing to final cuts, you develop confidence and ensure that each project phase meets the expected quality standards.
In conclusion, the road to mastering PVC sheet cutting lies in balancing practical experience with informed expertise, leaning on authoritative sources, and persistently striving for trustworthy practices that guarantee both material longevity and precision in application. This multifaceted approach ensures that each PVC piece not only meets size specifications but also enhances the integrity and aesthetic of the finished project.