The PVC production industry plays a pivotal role in the global economy, providing materials essential for various applications ranging from construction to automotive sectors. As one delves into the intricacies of PVC (Polyvinyl Chloride) production, it becomes clear that achieving high-quality output requires not only state-of-the-art technology but also a deep understanding of chemical processes. This article demystifies the journey of PVC from raw materials to finished products and explores what it takes to optimize production for quality and efficiency.
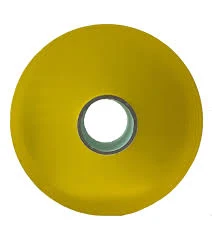
Polyvinyl Chloride, or PVC, is a synthetic plastic polymer produced through the polymerization of vinyl chloride monomer (VCM). The journey begins with ethylene, derived from natural gas or petroleum, which reacts with chlorine to produce ethylene dichloride (EDC). When EDC undergoes thermal cracking, it yields vinyl chloride monomer. It’s this hydrocarbon derivative that forms the basis of PVC. Successful conversion of VCM into PVC requires maintaining optimal conditions in a polymerization reactor, a process fine-tuned through years of chemical engineering ingenuity.
The production of PVC is distinctly characterized by suspension polymerization—the most widely used method. Utilizing water as a dispersing medium, the VCM is mixed with water and suspended using a stirring apparatus. Free-radical initiators like peroxides are introduced to begin the polymerization process, transforming the VCM into polymer chains. This results in PVC resin in the form of white powder upon drying. The entire operation demands a meticulous balance of temperature, pressure, and initiator concentration to ensure high-grade PVC with desired molecular weights and properties.
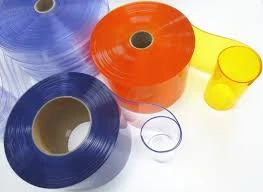
Quality control in the production of PVC cannot be overstated. The polymerization process is susceptible to several factors, including temperature fluctuations and contaminants that could lead to polymer defects. To uphold high standards of quality, modern production facilities have embraced automation and real-time monitoring systems. Integrating spectroscopic techniques and chromatographic analysis allows for the continuous assessment of VCM conversion efficiency, ensuring the polymerization process proceeds uniformly.
A common derivative of PVC production expertise is the understanding of plasticizer incorporation to produce flexible PVC. This variant is particularly significant in applications requiring elasticity, such as cables and hoses. By blending PVC with varying amounts of plasticizers, manufacturers can create a versatile material with tailored properties for different industrial needs. For instance, dioctyl phthalate (DOP) and diisononyl phthalate (DINP) are major plasticizers that enhance flexibility without compromising the material’s durability.
pvc production
Environmental stewardship and safety are key drivers of innovation in the PVC production sector. Traditional production techniques have been scrutinized for their environmental impact, particularly the emission of chlorinated compounds. In response, the industry is witnessing a surge in research focused on the development of sustainable production methods. Advances in cleaner EDC production, solvent-free processes, and recycling technologies highlight the ongoing shift towards more eco-friendly approaches.
Safety protocols are equally critical, with stringent measures implemented to prevent accidents due to the volatility and flammability of the raw materials involved. Modern PVC production practices emphasize robust safety training, emergency response preparedness, and rigorous equipment maintenance schedules. Automation also plays a role in enhancing safety by reducing human exposure to hazardous conditions during the polymerization process.
In terms of market dynamics, the demand for PVC continues to grow, largely driven by its broad applicability and economic advantage over other polymers. This surge necessitates that manufacturers scale their operations efficiently while maintaining product quality. Experience in optimizing production lines is crucial, as is expertise in implementing lean manufacturing techniques to reduce waste and improve throughput times.
Furthermore, navigating regulatory frameworks is essential for any PVC producer looking to expand their market reach. Understanding global standards, such as those set by the European Union for REACH compliance (Registration, Evaluation, Authorization, and Restriction of Chemicals), is paramount. Comprehensive compliance not only ensures market access but also builds trust with eco-conscious consumers increasingly focused on sustainability.
In summary, excelling in PVC production requires a harmonious blend of technical expertise, commitment to quality, environmental responsibility, and adherence to safety standards. As the industry evolves, those who harness innovation and adapt to ever-changing market demands are poised to lead in a future where sustainability and efficiency are at the forefront of manufacturing excellence. PVC's versatility and economic advantages ensure its continued prominence in the material world, as long as its production aligns with the principles of safety, environmental stewardship, and cutting-edge technology.